With most of the wings complete at the end of last February, I clad the sides of the nacelles with 2mm depron and the underneath with 2 layers of 6mm, to give them some resilience when landing. The shape of the front of the nacelles is quite complex, so it took a few tries before I got them looking right. This is the big advantage of depron in that it can be sanded and carved very easily. Even so, there is a lot of triangular strip inside there to keep all the bits in the right place!
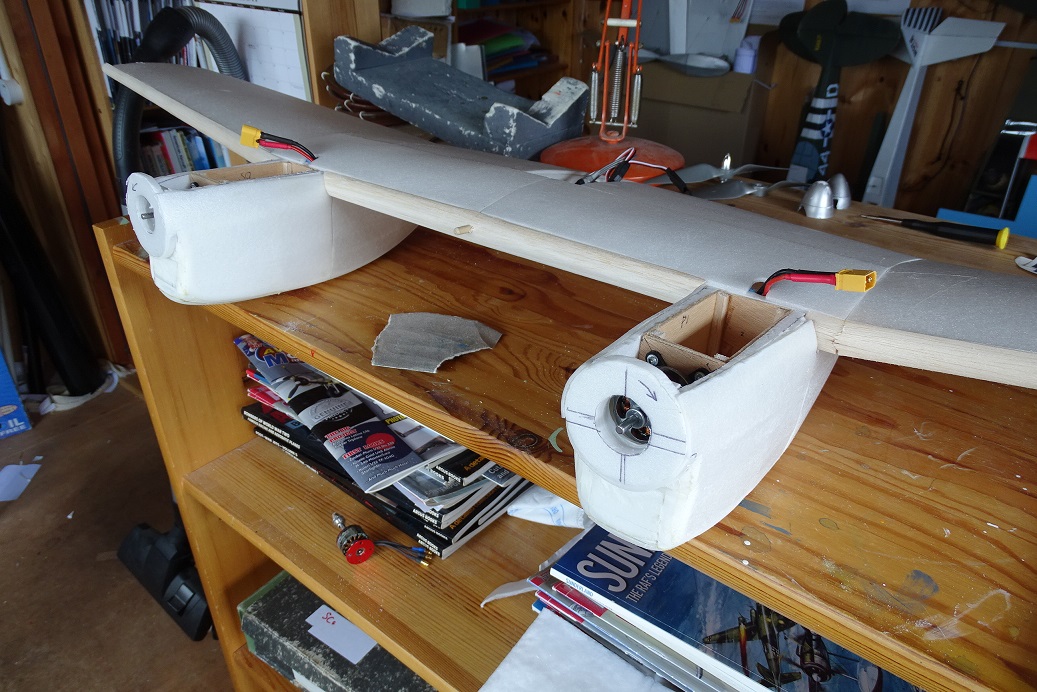 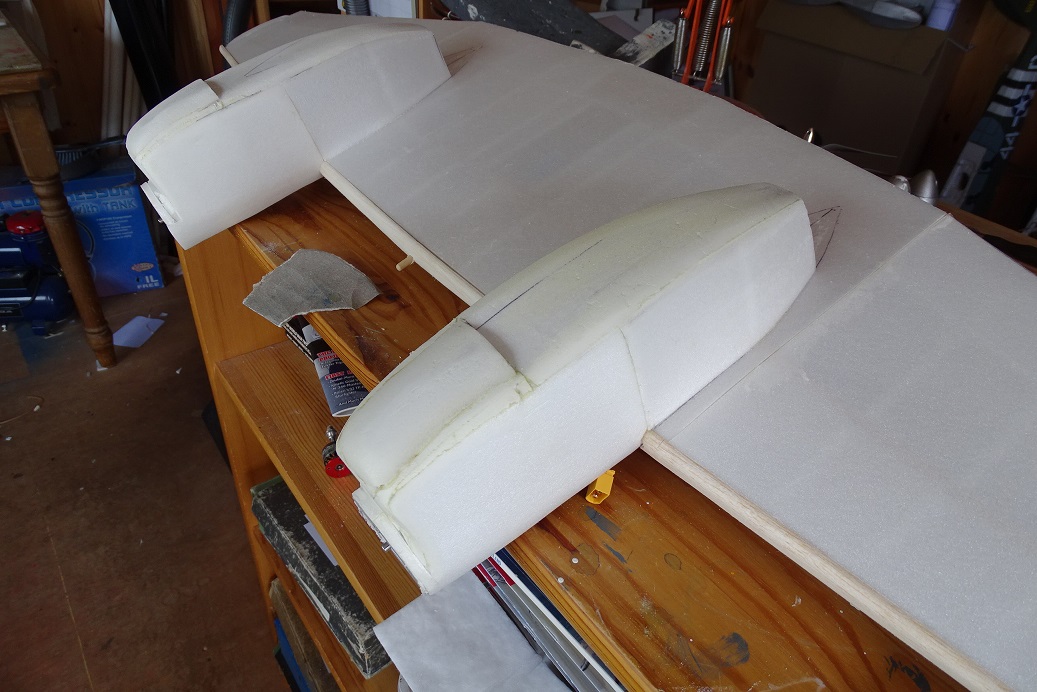
With these parts at the 75% stage, I turned to the fuselage. Its core is a depron box, just thin and tall enough to fit inside the outer skin of 2mm depron. Given the Beau’s shape, this is much taller than it is wide, so there is a fair amount to do to get the shape right. Here’s the basic shape with some very simple formers in place, then with the other side and the scale shapes glued on the outside and finally with the wing slotted into place for a rough assembly test..
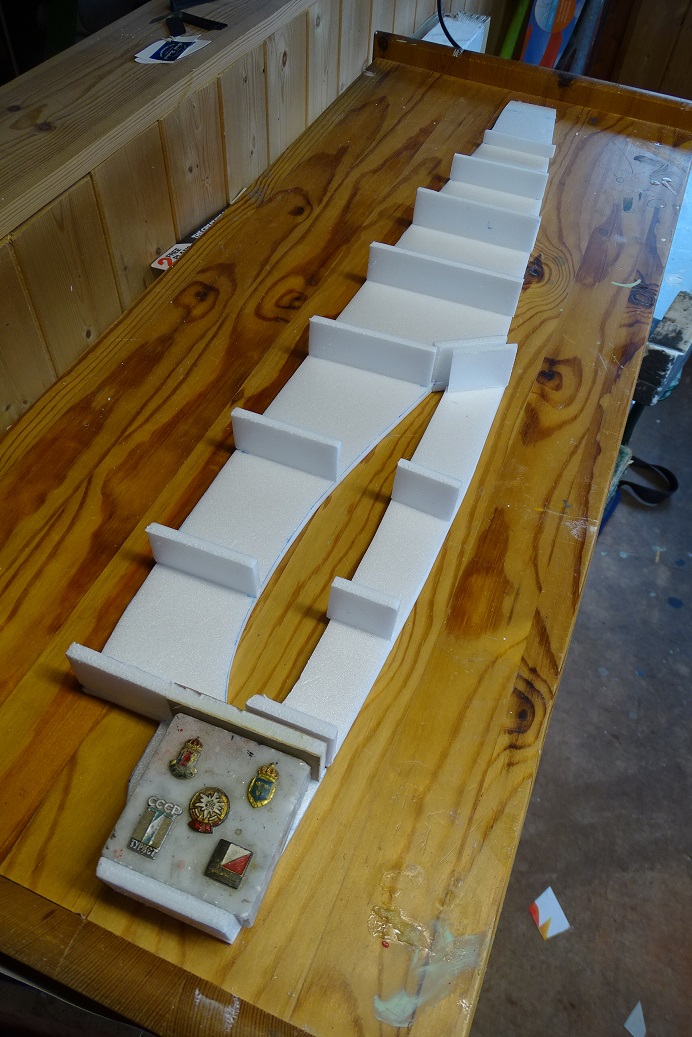 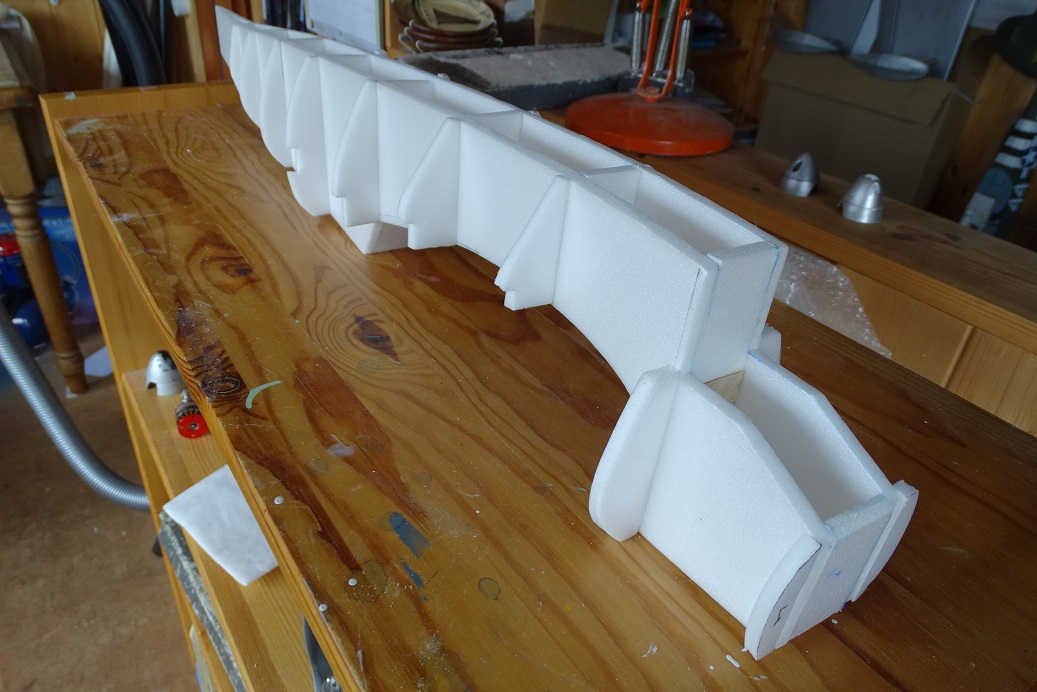
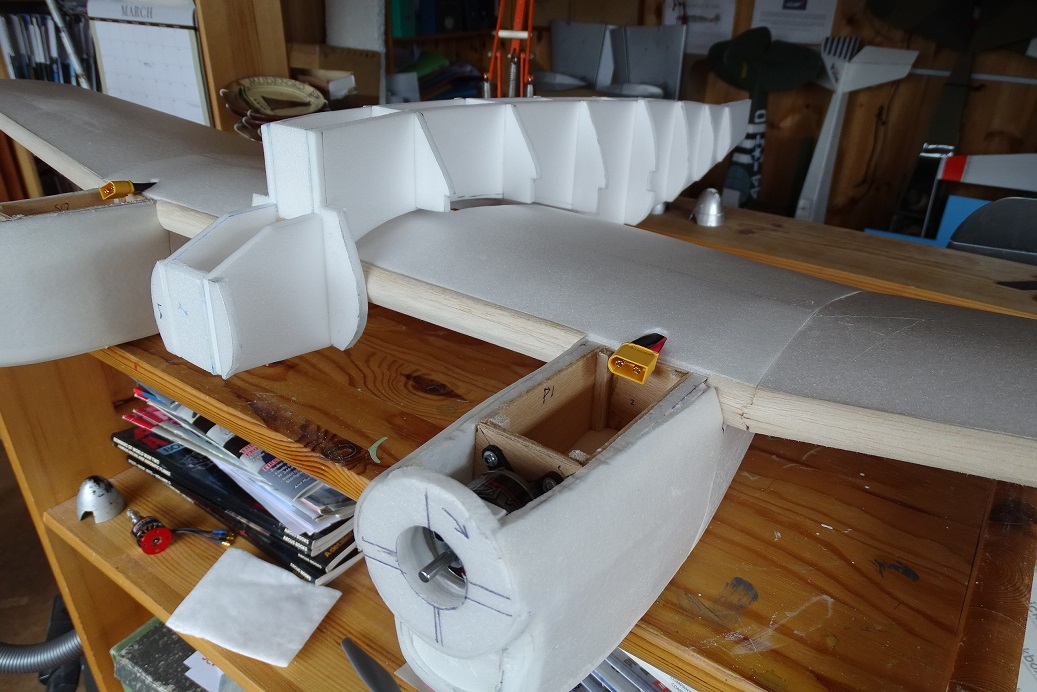
You can see that my wing profile didn’t quite match up with the fuselage, so a bit of sanding and cutting was needed before it all fitted together. Even then, I had to add a slice of depron to make the join “invisible”. The top and bottom 6mm sheet has been added and the fuselage is almost ready for its skin of 2mm.
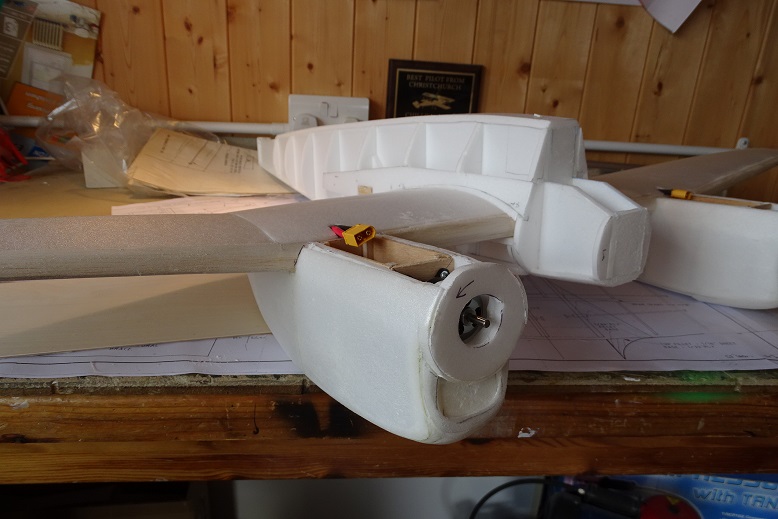 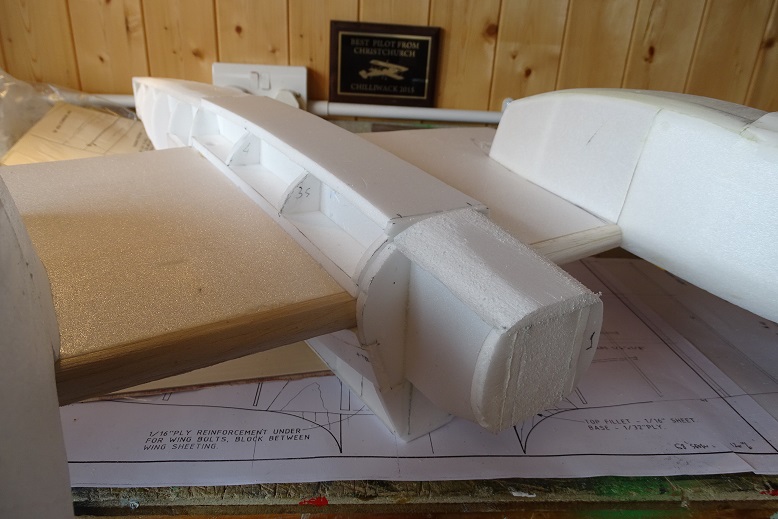
A word of explanation about the wing peg and bolt attachment and the lower fairing. Originally I made the fairing detachable, but it became obvious that if I was the be able to solo hand launch, it had to be fixed or it would just fall off. Hence the belt and braces of two pegs and a magnet. The captive nut plate was epoxied in place and amazingly the bolts lined up first time.
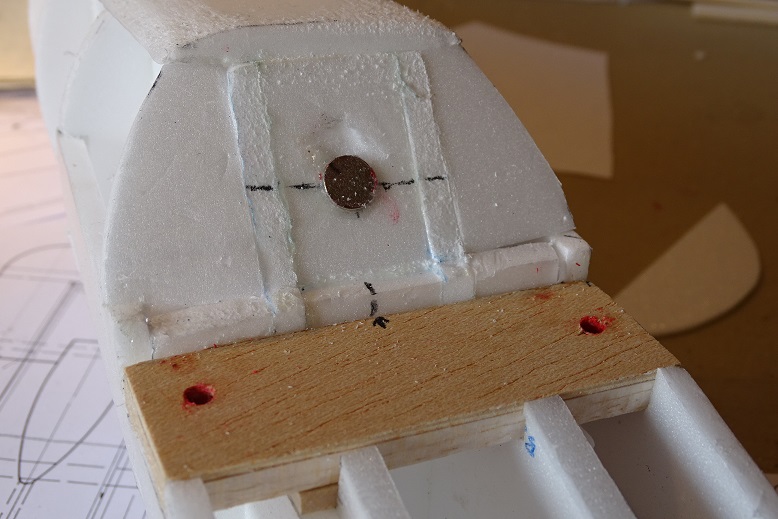 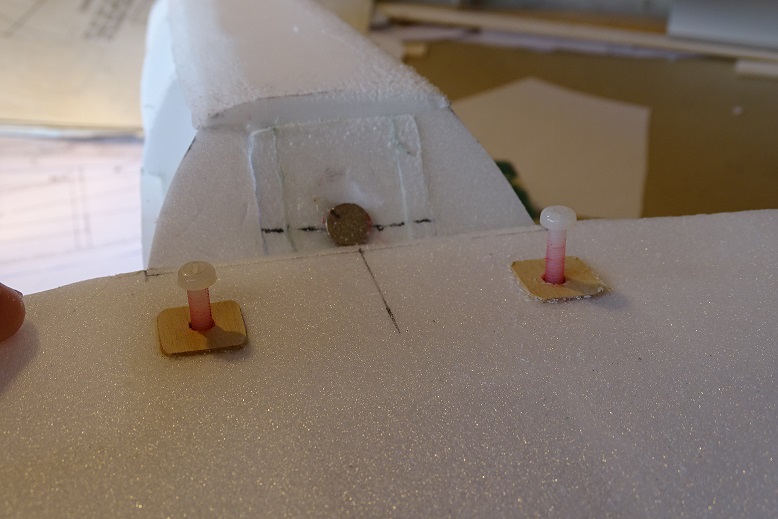
The elevator servos were fixed inaccessibly - this could be a mistake! Two are needed because each elevator half must be driven separately. The dihedral tailplane was needed to correct directional instability caused by the forward area of the Merlins, but was eventually adopted across all marks of Beaufighter. A Sullivan micro system was used for the linkages.
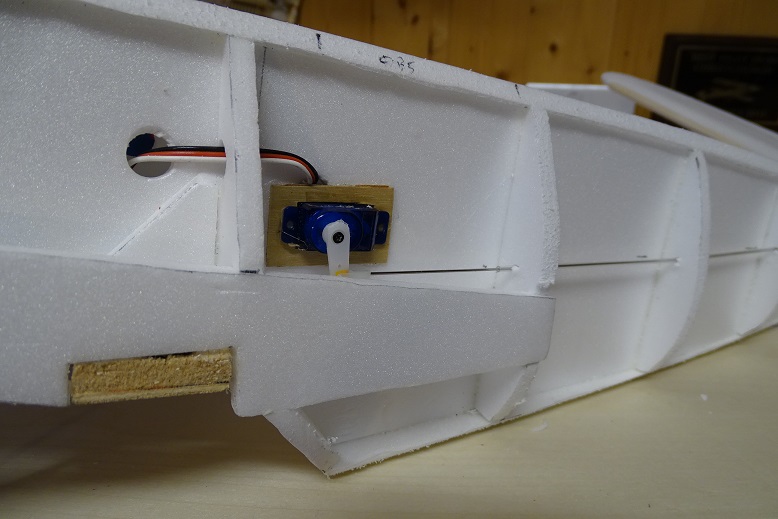 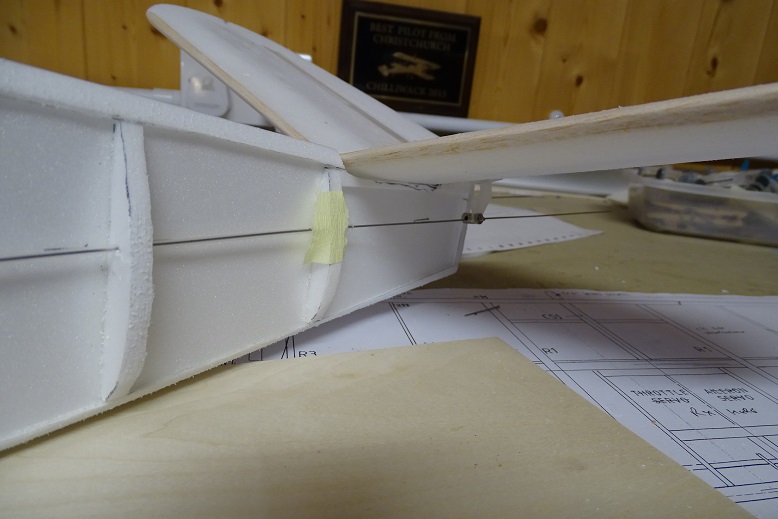
Skinning the fuselage with 2mm depron was easy enough, using paper patterns to cut the critical areas accurately and then sanding the top and bottom with a block to get it to follow the the 6mm sheet. The thin 2mm sheet can conform to slight dual curvature without too much trouble. UHU Por used as contact adhesive was perfect for this job.
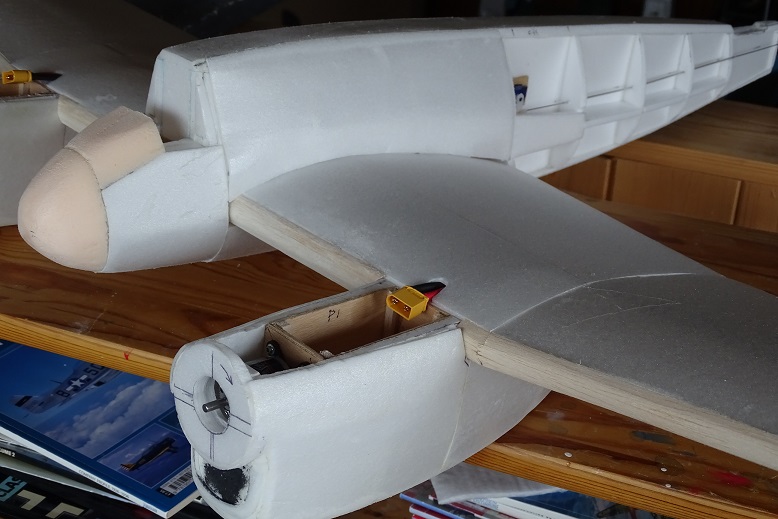 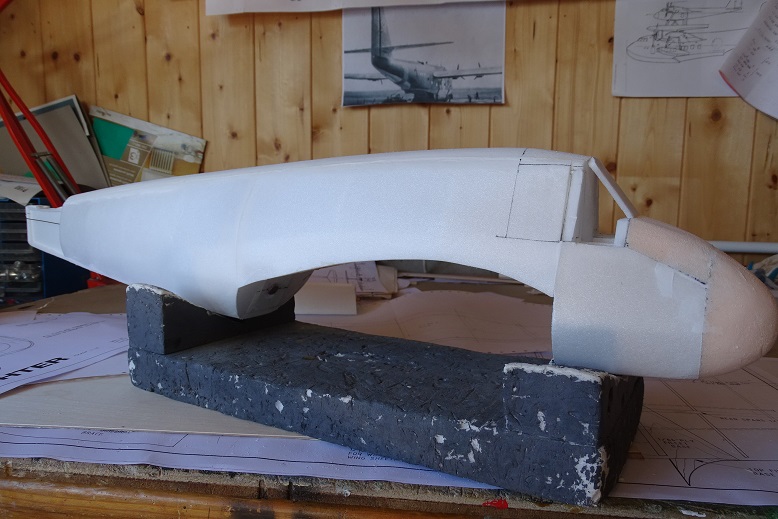
The nose cone, cockpit and observer’s dome are all pink foam, HWC, carved and sanded to shape. The dome needed an aperture to be HWC from the fuselage - all that careful work and then you cut a great hole in it! You can see that there is an additional layer of 6mm along the fuz top to bring it to scale size and shape. This was always the plan, but it very nearly got forgotten in the rush to finish off. Almost the whole model was covered in tissue from a stash of Esaki (Mike Woodhouse free flight supplies), with a coat of DeLuxe Models Eze Kote *rolls eyes* all over, followed by a light sanding, then the tissue applied damp, with more Eze Kote. I somehow forgot to cover the top of the tailplane and the fin and rudder, and as a results they look and feel rough as a badger compared with the wing, nacelles and fuselage. Hiding the tissue join and edge lines is possible, but tricky. I do strongly recommend covering these models with tissue: it adds a bit of strength and ding resistance and gives a decent smooth surface for painting.
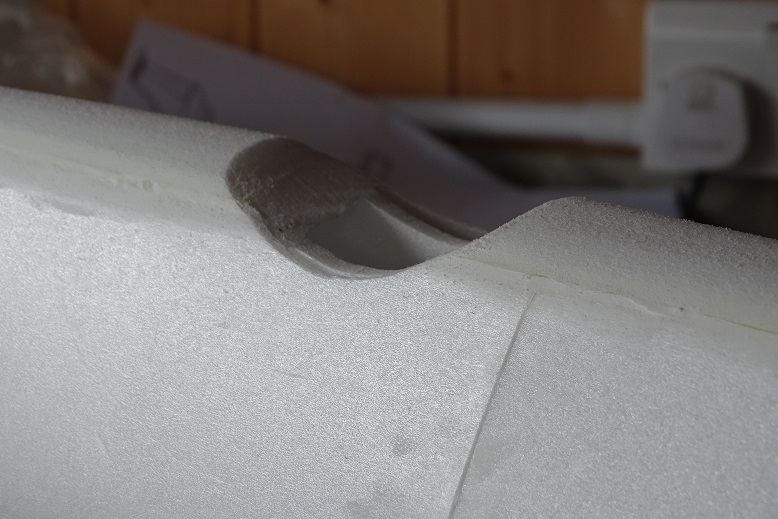 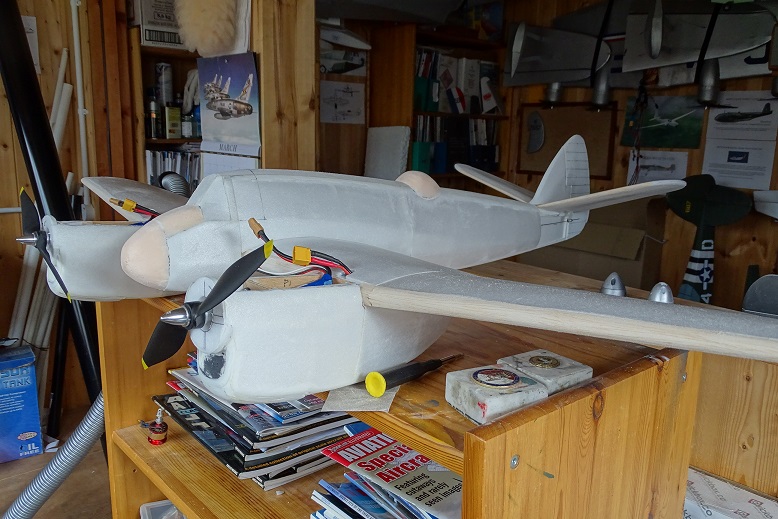
At last I could roller on the matt black to hide all those joins and edge lines. It was ridiculously easy to do but needed two coats before I got a decent solid finish. The cockpit was lined out with paper strips then painted gloss black, as was the dome. At this point all she needs before flight tests are the spinners, which are on order from RC Supplies. Oh, and balancing. I’ve made quite the error by having the batteries just behind the motors, one in each nacelle, and so I have to add weight to the tail.
Aaaargh!
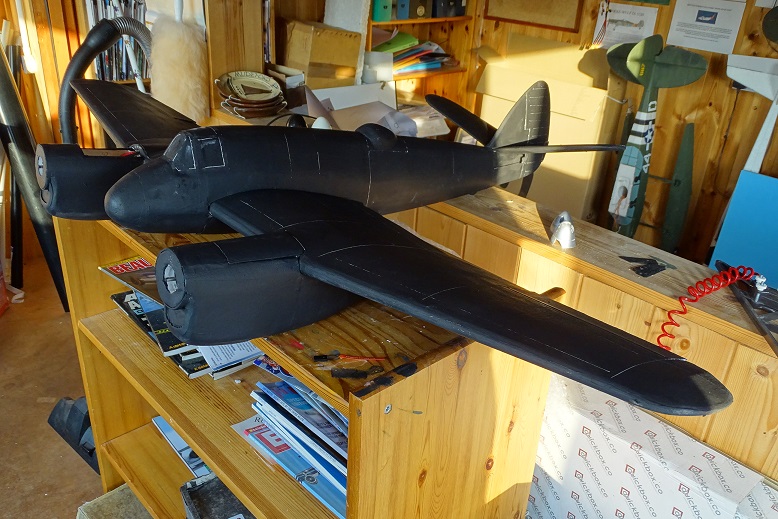 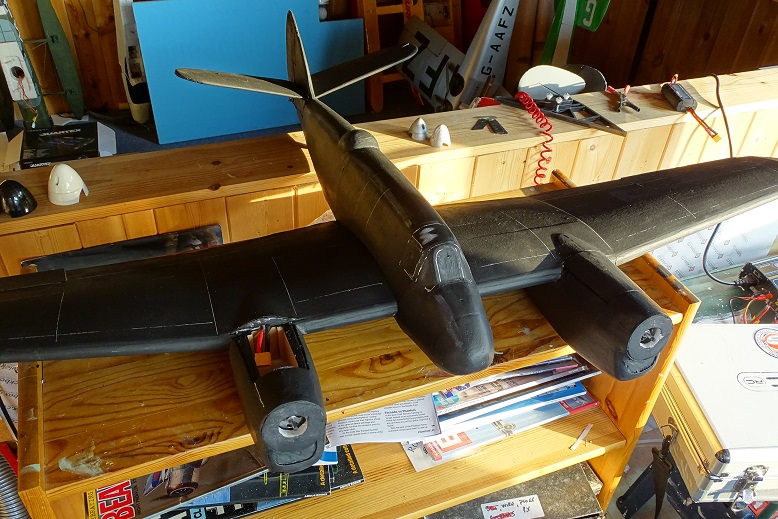
Just waiting for the markings now. In this state, with two 2-cell 1300 she weighs 2lb 1oz for a wing loading of about 14 oz/sq ft, so she will be quite a quick fighter.
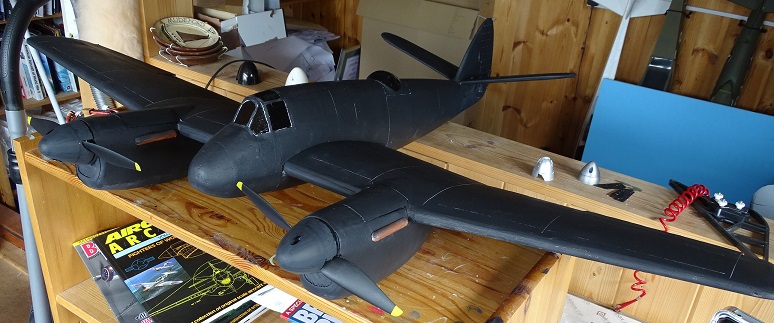
I got the markings from Callie Graphics in the USA. She has a very large range of ready-to-run markings (those on my Mustang were a stock item) but she will also cut specials like this one. Flash to bang time was about 2 weeks. The model looks much better with the roundels and lettering, obviously.
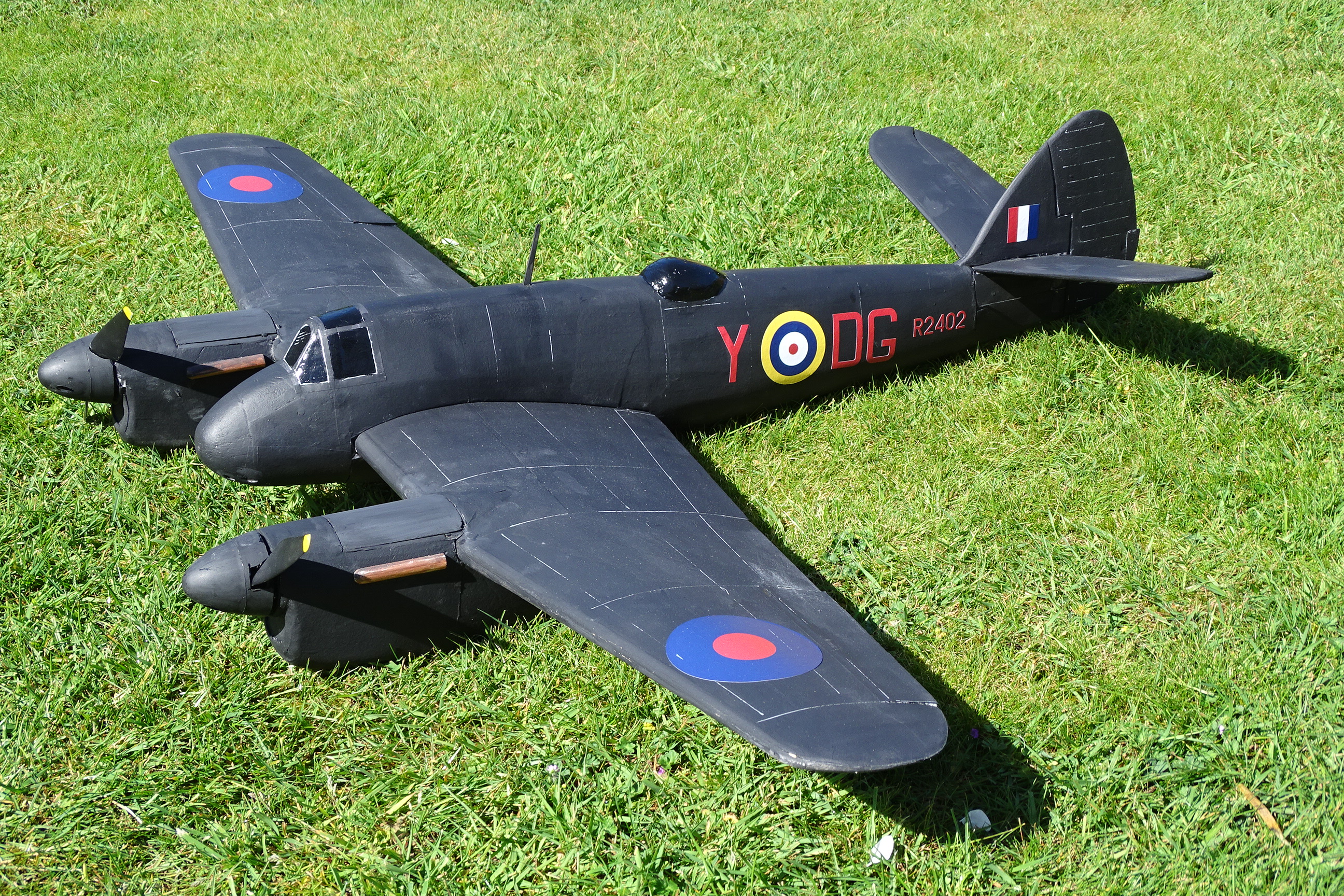
The maiden flight wtowards the end of April after a firm push by Tim Calvert, off she went and first impressions were that she flew very nicely. The motors were exceptionally quiet (“Whispering Death” indeed - but that was the Hercules version, not this Merlin-engined one). Up at height I tried a dive test for a CG check and it was obvious that she was tail heavy. I tried a sweep round over the horses’ field to land, but she stalled and spun into the grass. Oops. The only damage was to the starboard motor mount (2 laminations of 3mm liteply) which was easily replaced and epoxied onto the bearers with the re-fitted motor. A lick of paint later and she was ready to fly, AFTER removing half an ounce of lead from the tail.
The next day she flew perfectly from a hand launch and after 5 minutes of very pleasant flight, skidded gently to a halt near my feet.
Specs:
Beaufighter MkII night fighter, from a 1990 free plan in FSM, converted from balsa and ply and twin .10 IC motors.Span 48”, weight 2 lbs or so, All depron except for the mainspar and motor mounts. Two Park 450 motors with 17A SCs and 9x6 handed props. Paint by Dulux, markings by Callie Graphics, design and build by Mike Roach.
|