Changing a shaft on a brushless motor
by Tim Calvert.
At some stage most flyers will be faced with fitting or altering a shaft on a brushless motor, whether it be replacing a bent shaft after that landing incident, or reversing a shaft to allow a firewall mounted motor to be front mounted in a glider.
Stage 1: loosen the hex Allen fixings, you will find at least one fixing that fixes the rotating can part of the motor to the shaft, some brands have two. Most seem to be a 1.5mm hex
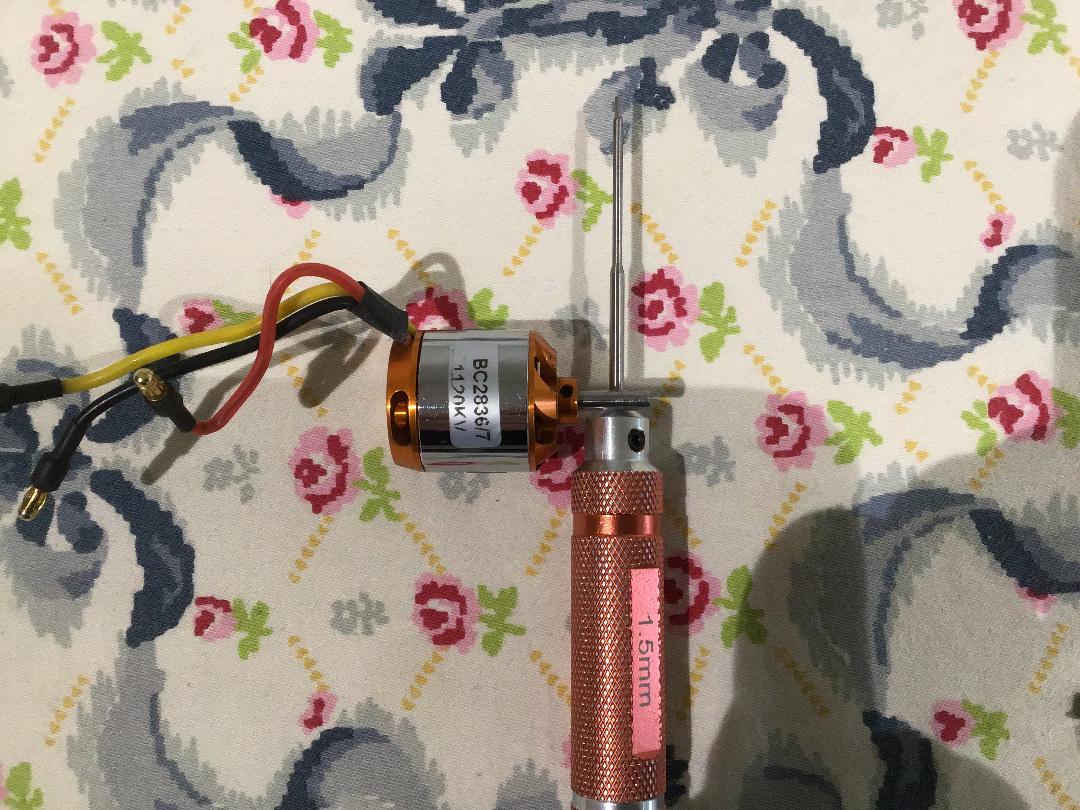
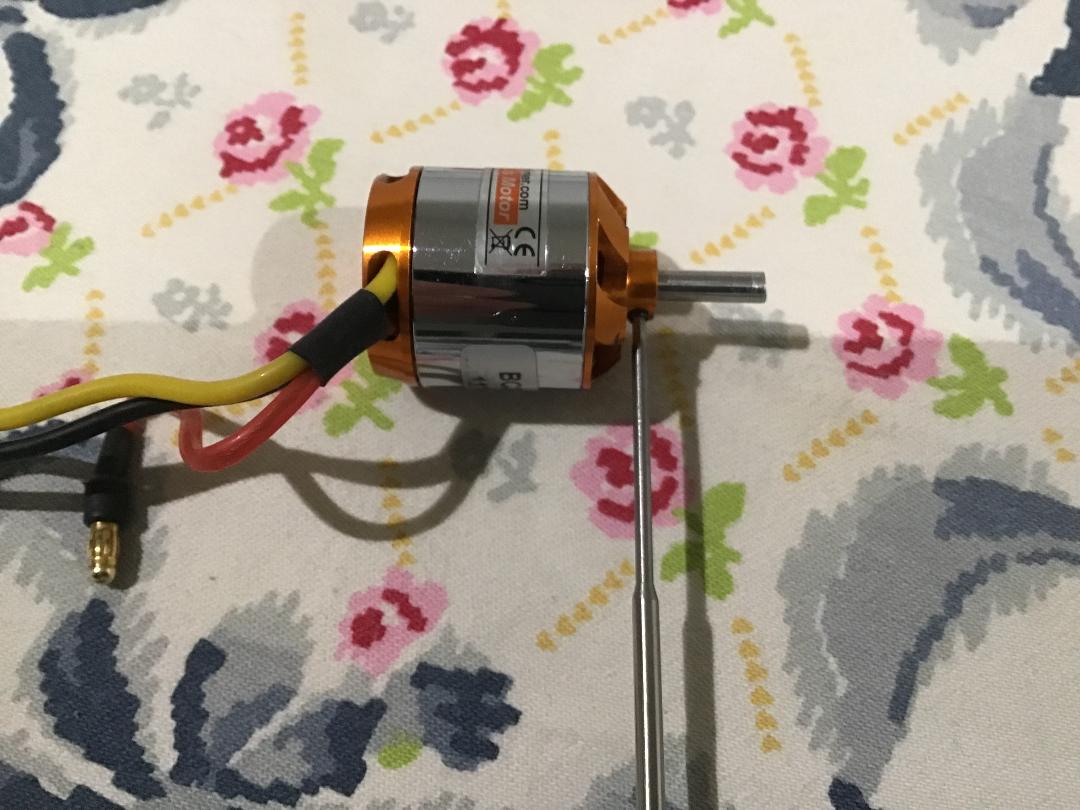
Stage 2: remove the circlip/eclip that retains the shaft at the fixed end of the motor. Just take care and do it somewhere where you can find the clip when it springs off to disappear in the carpet. You will probably find a small washer that was between the clip and the bearing.
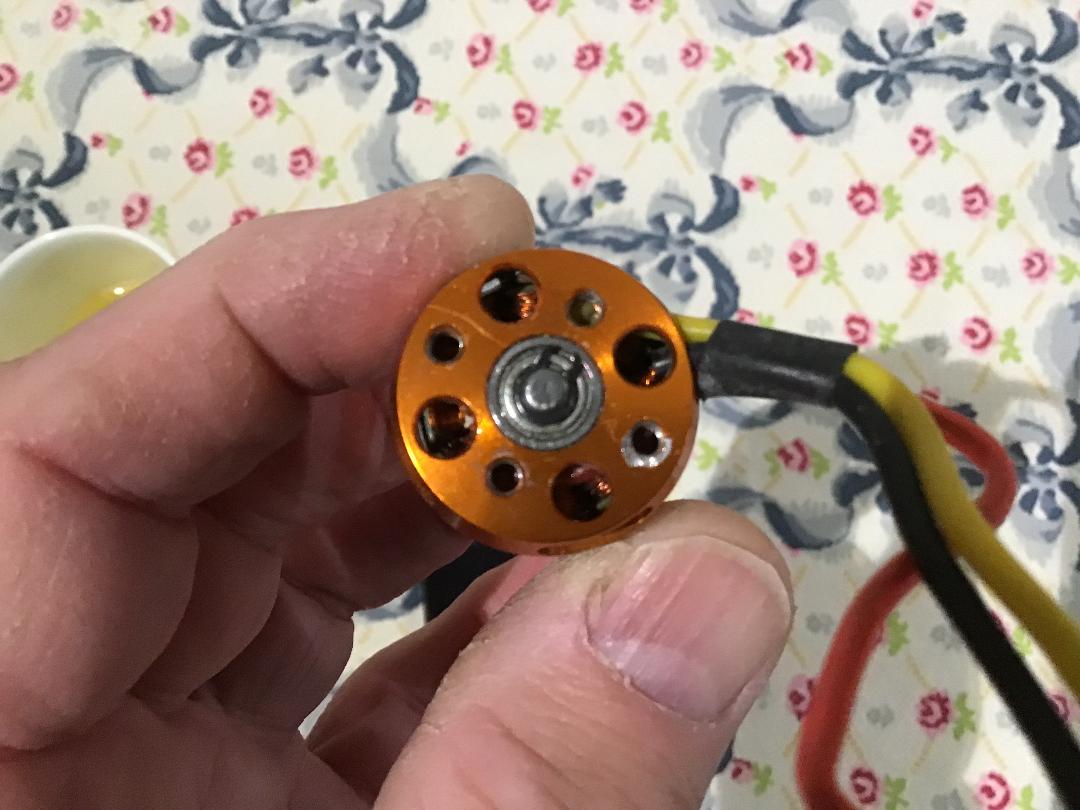
Stage 3: separate he can part of the motor from the fixed part, you will have to overcome the magnets so some some pressure may be needed . There may be additional washers on the shaft between the motor parts and bearing surfaces, note where they go.
Stage 4: tap out the shaft, with a suitable drift, an old shaft or drill blank make suitable drifts, placing the motor of vice jaws or a lump of wood with hole drilled in it make suitable surfaces to hold the motor can and allow the shaft to protrude.
Stage 5: tap in the new shaft, make sure the circlip groove is at the correct end, do not use excessive force or you bend the new shaft.
Stage 6: reassemble the motor, reversing stages 3 to 1, make sure that the flats on the shaft line up with the hex screws.
Stage 7: congratulate oneself on job well done, Go get a cup of tea.
If you are reversing a shaft, front mounted motors will require a shaft with circlip groove part way down the shaft to allow the shaft to protrude, firewall mounts have the groove at the shaft end, many brands provide ambidextrous shafts with two grooves allowing you the choice. If you are unlucky You may need to acquire a suitable shaft or cut an additional groove.
Sources of shafts.
HobbyKing.com, rctimer.com and Robotbirds,com stock a wide variety of replacement shafts, as long as the shaft is the correct dia and length they will generally fit, more care may be needed with a front mounted motor to ensure the correct location of the circlip groove, longer shafts can always be cut to length.
If you are really stuck or need a custom shaft you can make your own from a length of silver steel, a 330mm length costs only £3 or so from many vendors on eBay , enough for 5 or 6 shafts, Club members Ken Stokes and John Davies both have lathes and may be persuaded to cut the circlip grooves for you. Most shafts are 3mm, 4mm or 5mm in dia, there are some motors that have 1/8 (3.17mm) so take care if it one of the smaller diameter shafts, flats can be easily ground in with a dremel or filed, fix the shaft in a vice first to secure.
|