The Multiplex Pilatus Porter and single axis piezo gyros.
by Adrian Sharpe
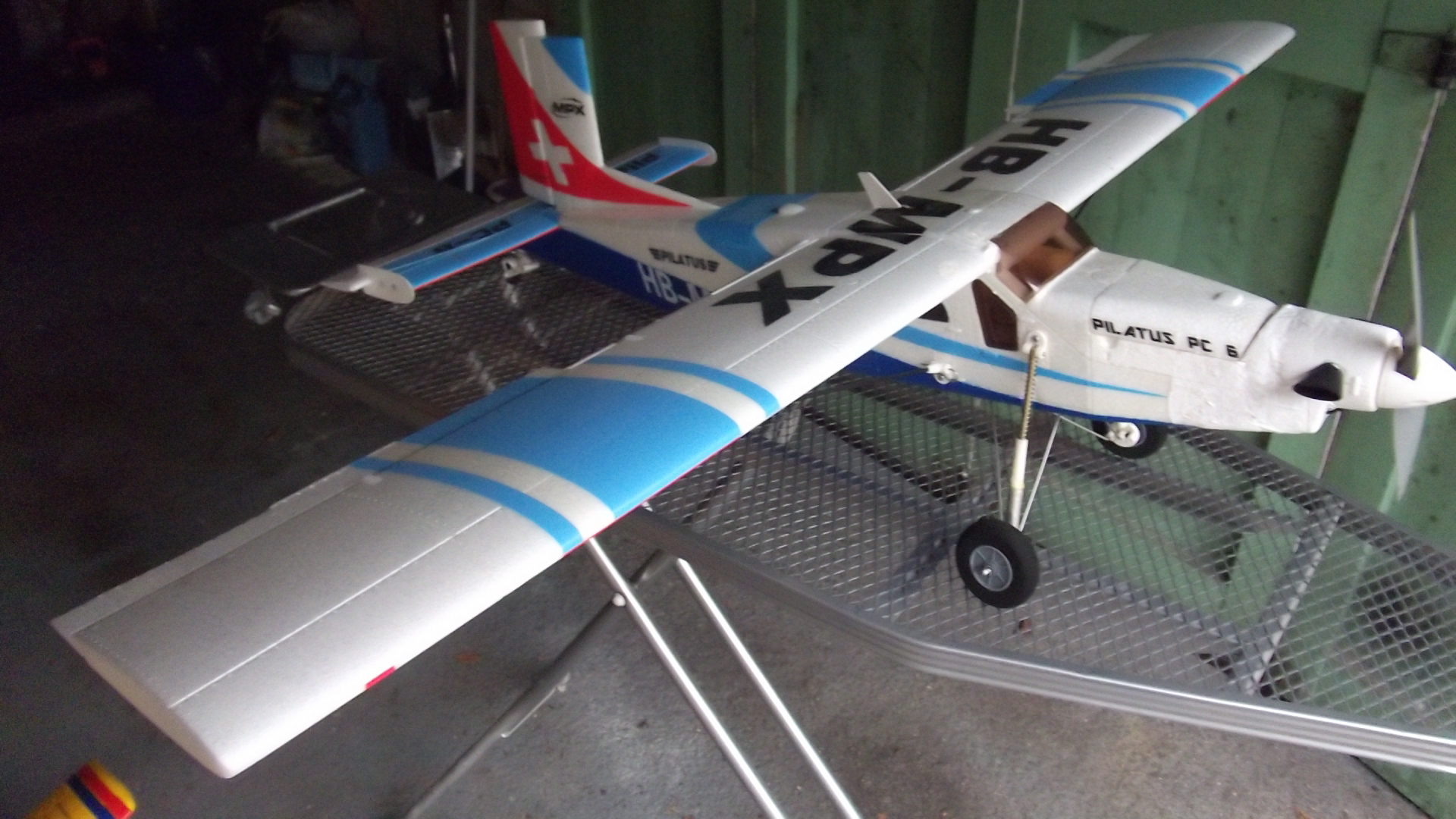
I have been flying my Multiplex Pilatus Porter for a season now over the Phoenix Model Flying Club (Dorset) site on the Trigon Estate near Wareham.
The Pilatus Porter comes with motor, ESC and all servos fitted so that only a receiver and the battery are required to go flying. Overall, it is a very nice model to fly; it is very aerobatic and quite similar to a WOT4 in the air. It would complete the “B” Test routine easily.
Unfortunately it is not unusual with ARTF models to find a few issues during initial flying and my experience with the “Porter” was no different.
The problems I found with my model included a weak undercarriage and an extremely quick roll rate.
Perhaps if the model was flown from tarmac or a super smooth grass strip the relatively weak undercarriage would not be an issue, but the models undercarriage assembly includes several plastic moulded components which have all broken in service.
I found shrinkage voids where breaks occurred in two components and therefore it was necessary to replace them with metal rods. Two more plastic components broke around a weak spot in the moulding so I glued aluminium sleeves around those areas to build in some strength. So far so good.
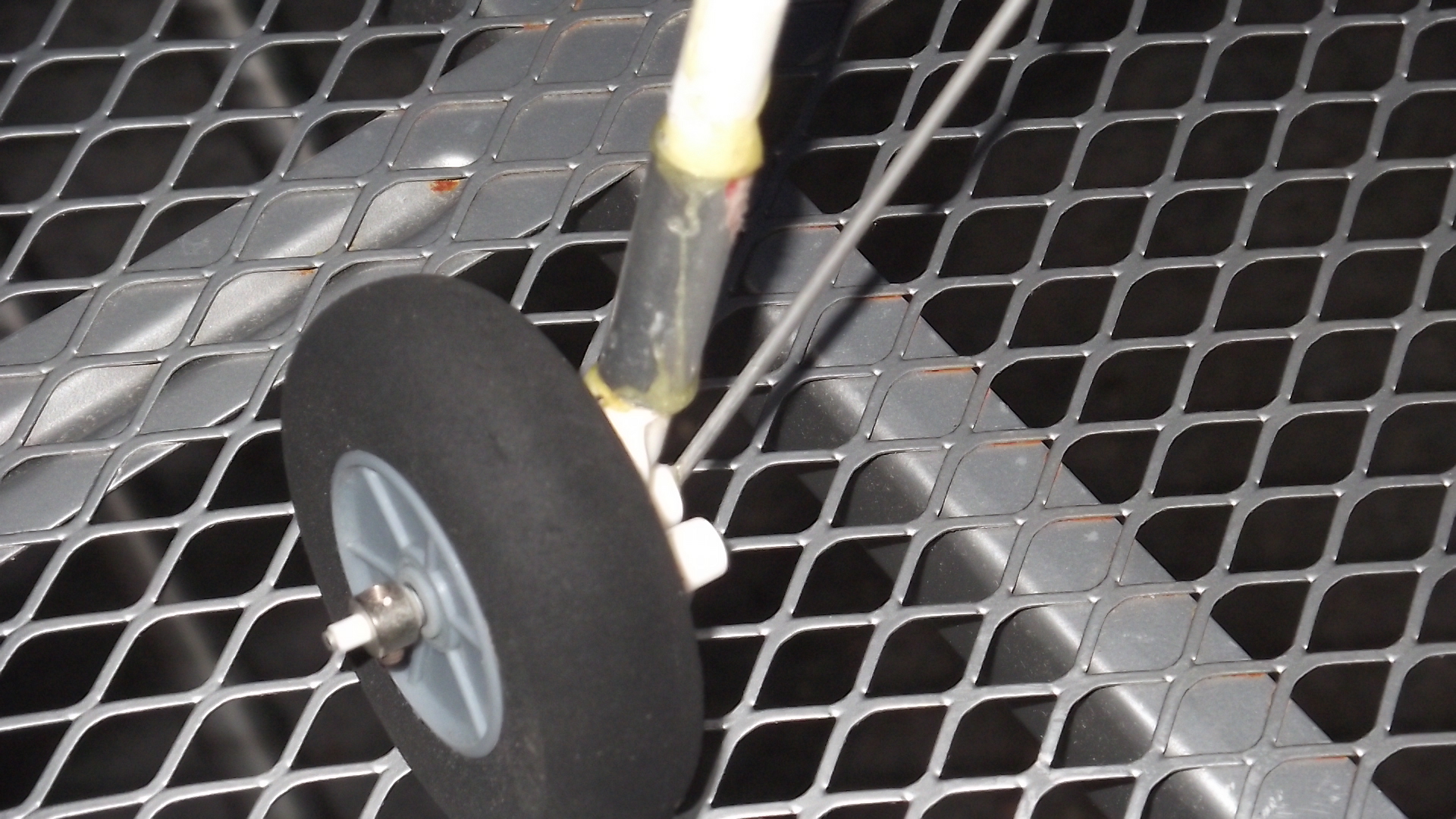 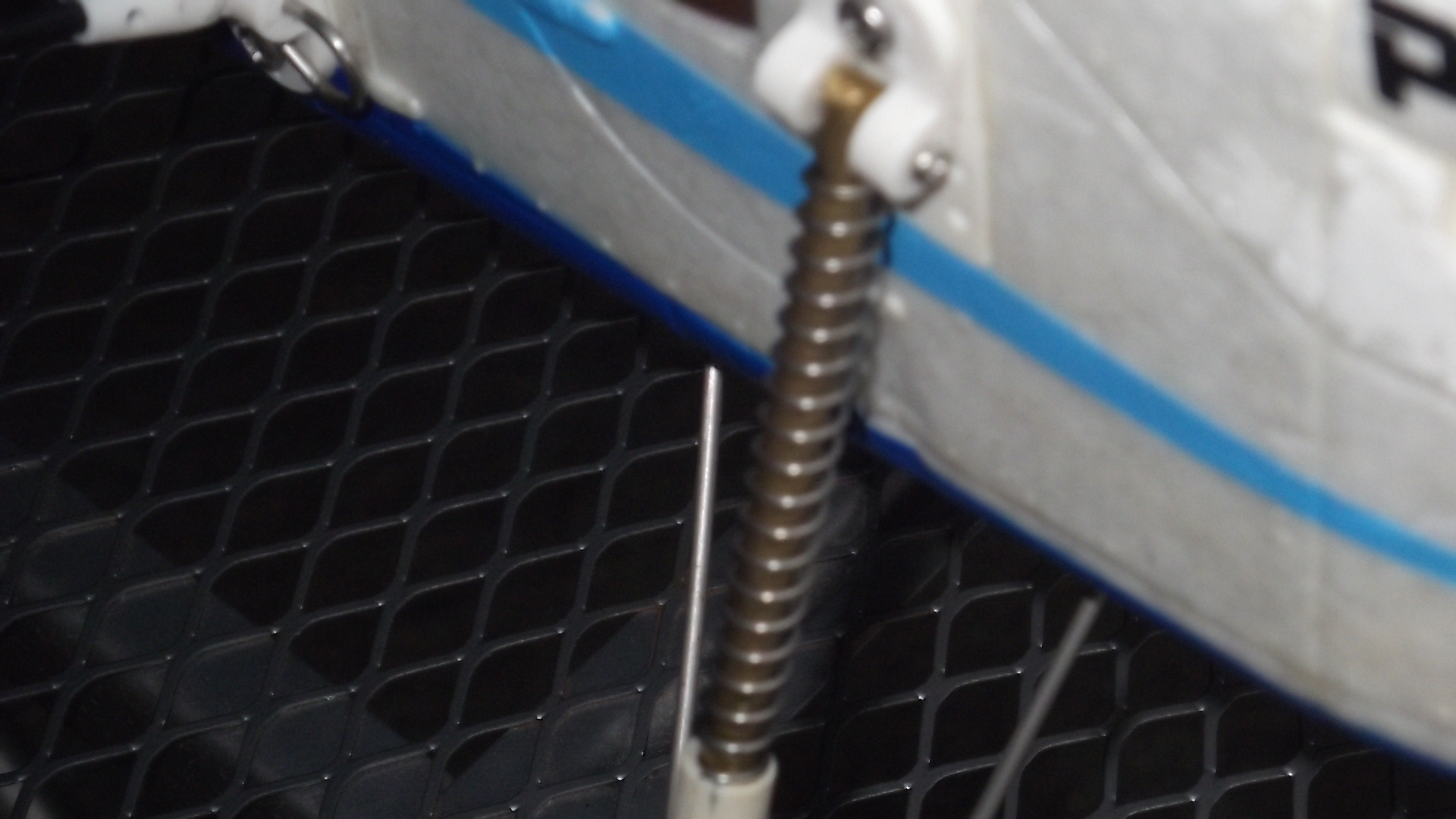
As far as the high roll rate is concerned – my solution has been to fit a GWS single axis piezo gyro. I have used these units before to cure tail dragger models of ground loops and in my view they are handy devices to have around.
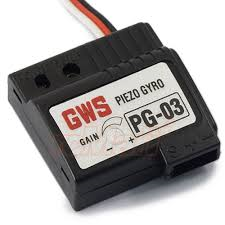
These solid state piezo gyros do not contain gyroscopes but act like rotational accelerometers. They are connected between the receiver and servo and modify the length of the servo control pulse according to the rate of rotational/angular acceleration detected around its operating axis. In the case of my ‘Porter, I installed the piezo gyro so that its operating axis was parallel to the fore/aft axis of the model. In this orientation the device is sensitive to roll rate and so when the model/piezo gyro rolls to the right, it changes the servo control pulse so that either the aileron movement to the right is reduced or if the roll rate is severe, the ailerons will oppose the right roll. The degree to which the piezo gyro affects the servo pulse length is set by the “gain” control on the device which you set yourself. The higher the “gain” the more the device will react to roll rate and the slower the model will roll in flight.
In installations on my Flair Scout models – SE5a, Puppeteer and Fokker Triplane, the piezo gyros were mounted with their operating axis vertical in the airframe so that they would react to Yaw. If the model swung to the left or right during take-off/landing the piezo gyro would operate the rudder to oppose that swing and keep the model running straight.
I appreciate that many handling issues can be resolved using the programming options available on modern transmitters, for example, most transmitters provide for exponential servo movement and also differential movement. I programmed in 60% exponential on the aileron control but the ‘Porter still proved a handful. Its response to elevator and rudder was fine but executing a nice smooth banked turn required constant nudging of the ailerons – not pleasurable for the pilot and not pleasant to watch because the model seemed always unsteady in banked flight.
After fitting the piezo gyro on the roll axis and setting the gain to 50%, the model is super steady; it will roll through 360 degrees now in about a second or two, rather than 4 twizzles per second before! Banked turns are relaxed and look good and the model flies in a nice scale like manner. Problem solved.
|